The Advantages of Liquid Silicone Injection Molding in Modern Business
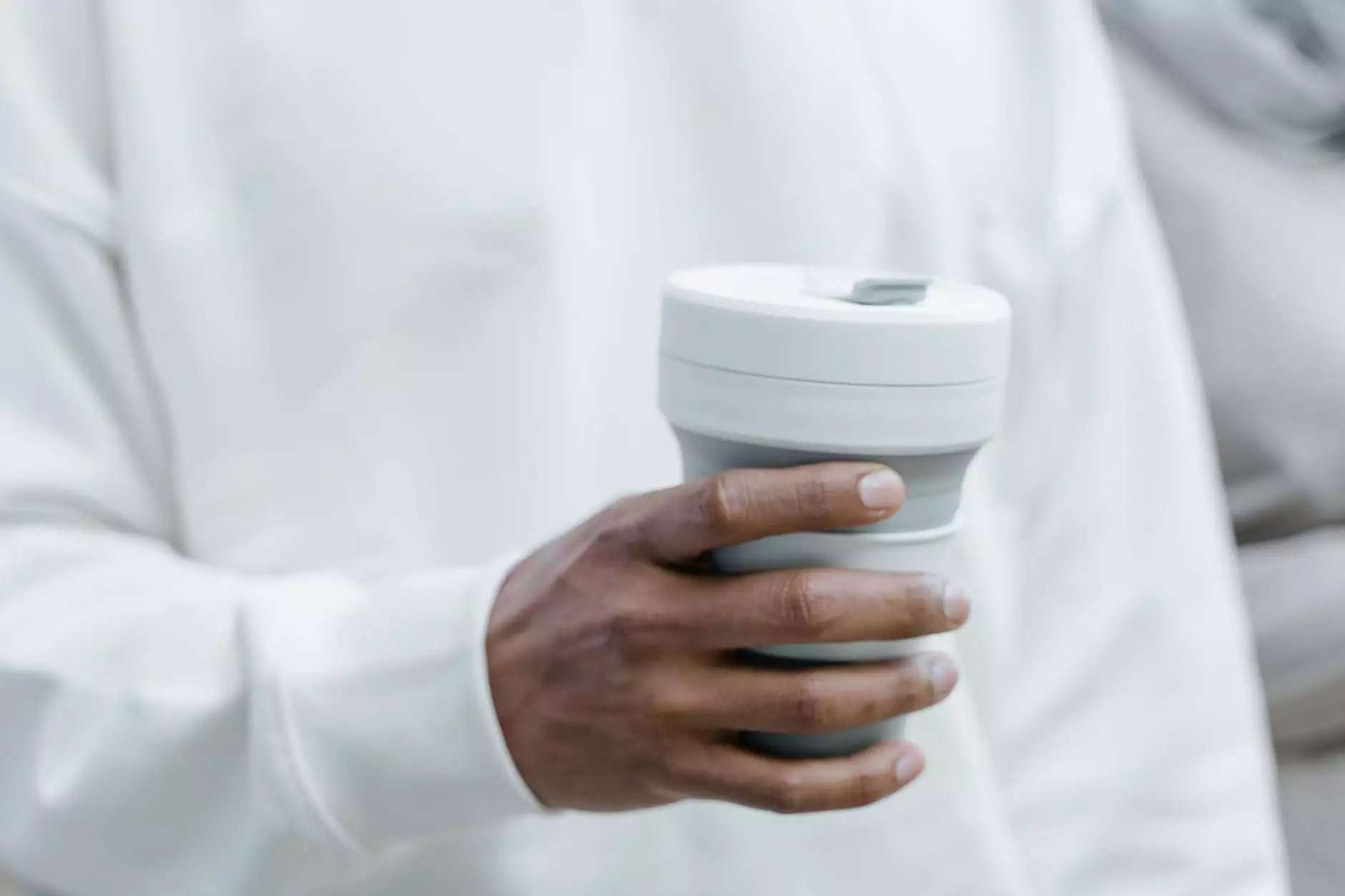
Liquid silicone injection molding is revolutionizing the way products are designed and manufactured, particularly in the high-precision domains of electronics and medical supplies. As businesses strive for innovation and efficiency, understanding the nuances and benefits of this molding technique is crucial for staying ahead in competitive markets. In this article, we’ll explore the ins and outs of liquid silicone injection molding and its impact on various industries.
Understanding Liquid Silicone Injection Molding
Liquid silicone injection molding (LSR) is a manufacturing process where liquid silicone rubber is injected into molds to create various components. This high-tech process is favored for its ability to produce flexible, durable, and chemically stable products. The following points highlight key aspects of the LSR process:
- Material Flexibility: Liquid silicone rubber can withstand extreme temperatures, making it ideal for various applications.
- Precision Engineering: This method allows for intricate designs with tight tolerances.
- Fast Production Cycle: LSR mold cycles are typically shorter than traditional rubber processes, allowing businesses to produce more in less time.
Key Advantages of Liquid Silicone Injection Molding
1. Enhanced Product Quality
One of the most notable benefits of liquid silicone injection molding is the high quality of products produced. The smooth surface finish and precise dimensional accuracy offered by the LSR process are essential for components used in sensitive applications, such as medical devices. This is crucial not just for functionality but also for the aesthetic appeal of the finished product.
2. Superior Durability
Components crafted from liquid silicone exhibit remarkable durability. They are resistant to UV radiation, ozone, and extreme temperatures. This makes LSR products the preferred choice for electronic devices that may be exposed to harsh environmental conditions.
3. Design Versatility
The design versatility offered by LSR is unparalleled. This molding technique supports a diverse range of designs, from simple to complex geometries. Designers and engineers can create multi-functional parts that incorporate multiple features into a single component, minimizing assembly time and improving overall efficiency.
4. Cost-Effectiveness
When it comes to long-term production, liquid silicone injection molding can be highly cost-effective. The rapid production cycles mean that businesses can manufacture large quantities of products in a shorter timeframe, reducing labor costs and increasing overall productivity.
5. Safety and Compliance
In industries such as medical supplies, compliance with safety regulations is paramount. Liquid silicone is non-toxic and biocompatible, making it suitable for medical devices that come into contact with the human body. This ensures that products not only meet stringent regulatory standards but also build consumer trust.
Applications in Electronics
The electronics industry has seen substantial growth in utilizing liquid silicone injection molding. Here are some common applications:
- Seals and Gaskets: Liquid silicone is often used for seals in electronic housings to protect against moisture and dust.
- Keypads and Buttons: The flexibility and tactile feel of silicone yield high-quality keypads that enhance user experience.
- Insulation Components: LSR serves as an excellent insulator for electronic components, offering protection from electrical interference.
Applications in Medical Supplies
The medical field is another area where LSR shines. Its applications include:
- Medical Devices: Many surgical instruments and implants are manufactured using liquid silicone due to its biocompatibility.
- Drug Delivery Systems: Silicone offers precision and reliability in creating components that facilitate effective drug delivery.
- Patient Monitoring Equipment: Measuring devices often utilize LSR for components that require repeated sterilization.
Environmental Considerations
With increasing pressure on businesses to adopt sustainable practices, liquid silicone injection molding presents an environmentally friendly option. The manufacturing process generates less waste compared to many traditional molding techniques. Additionally, LSR can be recycled, further contributing to a company’s sustainability goals.
The Future of Liquid Silicone Injection Molding
The potential for liquid silicone injection molding is vast, with ongoing advancements in technology and materials. Innovations like 3D printing integration and automated molding processes are expected to enhance efficiency and open new design possibilities. As industries evolve, LSR will undoubtedly play a critical role in meeting the demands of the future.
Choosing Nolato for Liquid Silicone Injection Molding Solutions
Nolato has established itself as a leader in the field of liquid silicone injection molding. Our commitment to quality, innovation and customer service sets us apart. We provide tailored solutions that meet the unique needs of our clients in the electronics and medical supplies sectors. By leveraging state-of-the-art technology and adhering to strict quality control standards, we ensure that our products not only meet but exceed expectations.
Conclusion
In conclusion, liquid silicone injection molding is a transformative technology that offers extensive advantages for businesses in the electronics and medical supplies industries. From enhanced product quality and durability to compliance with safety standards, LSR is shaping the future of manufacturing. Partnering with experienced providers like Nolato ensures you are leveraging this technology to its fullest potential, achieving greater innovation and efficiency in your operations.
As the landscape of manufacturing continues to evolve, the need for high-quality, flexible, and durable solutions will grow. Liquid silicone injection molding is not just a process; it's a gateway to superior product design and sustainable business practices. Embrace the future with confidence, knowing that the right choices today can lead to unprecedented success tomorrow.